Vent Silencers
Vent silencers are typically used in conjunction with relief or control valves on piping systems for compressed gases. When gas is released to atmosphere, it can create excessive noise that can be objectionable to surrounding areas. Dürr Universal has particular expertise as a supplier of steam vent silencers for industrial applications and natural gas blowdown silencers (BDS) for gas compression stations during emergency shutdown.
Vent silencer application areas
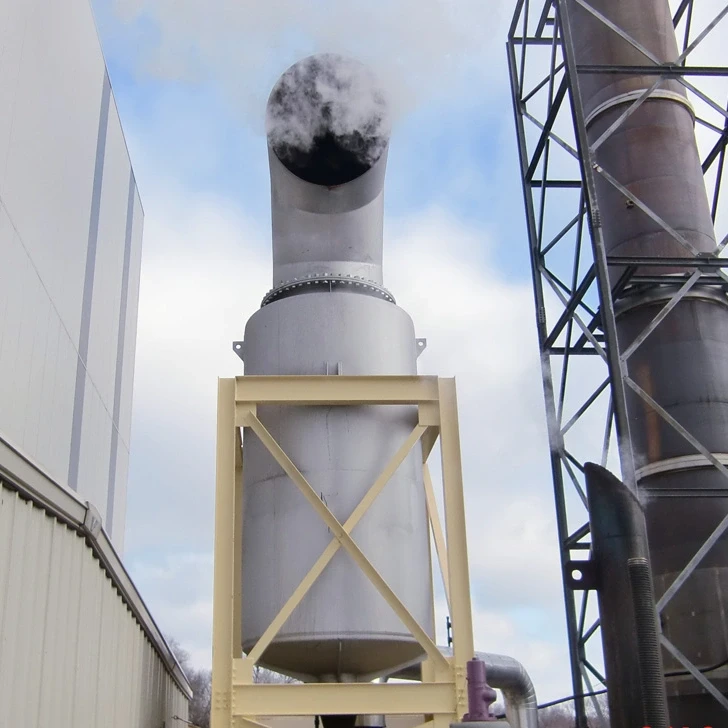
Typical applications for vent silencers include combined cycle power plant HRSG, oil and gas blowdown, industrial, chemical processing, and steam boilers. Dürr Universal’s vent silencers are used around the world in many applications.
Dürr Universal’s vent silencers effectively silence high-velocity air, steam and gas vents, as well as blowdowns to atmospheres in which sonic or critical flow conditions exist in the valve.
Typical pressure relief applications include HRSG units, steam boiler, super-heat headers, boiler startup and high-pressure purge air vents, natural gas blowdown, switch valves, compressor blow-offs, autoclaves and steam ejectors.
Vent silencer design
The concentric annular ring design and the wrapped Acousti-Tube vent silencer design offer a choice of silencer profile and configuration to meet site-specific requirements.
Vent silencer inspections
Regular vent silencer inspections are essential for employee safety and machinery performance. Proper maintenance of vent silencers is crucial not only for the equipment but also for the safety and well-being of nearby workers. A malfunctioning vent silencer can lead to increased noise levels, excessive pressure pulsations, or the release of harmful particles into the environment. Ensuring the proper functionality of vent silencers helps companies mitigate potential hazards and extend the lifespan of their equipment.
The following lists outlines the primary inspection parameters while on site:
- Check for corrosion or cracks - Inspect the welds on the inlet flange for any signs of corrosion or cracks.
- Examine flange bolts - Look for leaks that may be caused by loose flange bolts and tighten as necessary.
- Inspect welds - Check the weld from the head to the nozzle joint for integrity.
- Assess the lower head - Look for signs of cracks or rust on the lower head.
- Carefully look at external coatings - Inspect the shell-to-head connection for paint and rust issues.
- Evaluate paint integrity - Ensure the overall paint on the silencer is intact and undamaged.
- Check insulation - Look for deterioration in the external lagging and insulation.
- Inspect seam welds - Examine the seam welds along the overall shell for any defects.
- Monitor for natural corrosion - Regularly check for natural corrosion on the silencer.
- Identify thermal growth issues - Look for cracks caused by thermal expansion and growth.
- Check shell lugs - Inspect for cracked base material or welds at the shell lugs.
- Examine outlet/bird screen - Look for weld cracks, base material cracking, or corrosion at the outlet/bird screen.
- Inspect acoustic perf sheet - Check for deterioration of base material over the surface of perforated sheet.
- Assess perf welds - Inspect the attachment welds between the perforated plate and adjacent supports.
- Assess perf welds - Inspect the attachment welds between the perforated plate and adjacent supports.
- Check diffuser materials - Look for excessive corrosion on the diffuser perf cylinder, heads, and/or welds.
Having an industry expert assist with these inspections can help in the early detection of any deterioration, ensuring the safety and efficiency of the equipment.